Wood floor projects in residential complexes and buildings like apartments, townhouses, and condos can adversely affect all building occupants by particulate material and gases released into the air. Safety risks are increased as building occupants, and
people outside the crew are exposed to airborne contaminants due to close-quarter housing. It is unrealistic to move out tenants to perform renovation work, so alternatives need to be used for the health and safety of building occupants. Continue
reading to learn about these risks and how Basic Coatings is the solution.
Volatile organic compounds (VOC) are carbon-containing substances that become vapors or gases and assist with the application and drying of oil-based wood floor stains. VOCs are emitted into the air as soon as a can of stain is opened, as the stain is
applied, and as the stain dries. As the stain dries, the solvents evaporate and release the VOCs, which contribute to a strong solvent smell.
The odor is hazardous to people who smell it because exposure to the fumes can cause a burning sensation, blurred vision, and collapsing. Those who live in a residential complex may be affected by the fumes if a nearby neighbor is having their wood
floor stained.
Additionally, rags used to apply oil-based stains are at risk for spontaneous combustion if not properly stored or disposed of. As the rags begin to dry, the combination of heat, oxygen, and cloth can lead to an accidental fire, even without a source
of ignition. For wood floor stain projects taking place in a residential complex, this can be extremely dangerous to building occupants as well as homeowners. A fire will spread quickly and damage the building, other peoples’ homes, their
possessions, and potentially cause death.
"Waterbased stains are the best alternative to oil-based stains because water is used as the primary solvent."
The hazards that come from using oil-based stains can be eliminated by simply avoiding them completely. Waterbased stains are the best alternative to oil-based stains because water is used as the primary solvent. Therefore, the number of VOCs are
significantly reduced, and fire risks are eliminated. An alternative to oil-based stains is HyperTone™ Stains, a water/oil hybrid that provides unrivaled color penetration with all the benefits of a waterbased stain, including:
- Non-flammability, which allows stain rags to be disposed of or stored without special instruction
- Low odor, which avoids issues with offensive fumes
- Low VOCs, which increase sustainability and improve air quality
HyperTone Stains are extremely versatile with the ability to be used on sport, residential, or commercial wood flooring. Additionally, HyperTone Stains can be mixed to achieve many of the most popular colors in the wood floor industry. With 14 standard
colors, which include primary colors, there are countless ways to formulate the perfect color for any wood floor. Click here to view our HyperTone Color Gallery to see swatches of colors created by HyperTone Stains on 4 different wood species.
Wood Dust
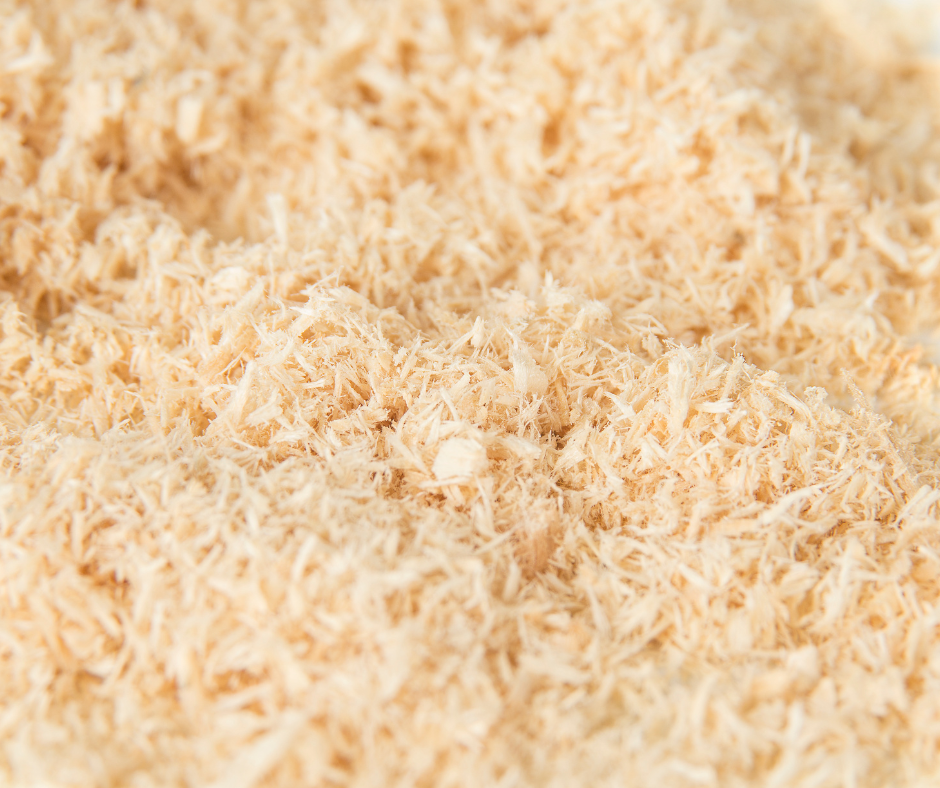
Wood dust is accumulated during every wood floor project, from sawing and routing to sanding and other operations. It becomes a potential health problem when the wood dust particles become airborne. Exposure to wood dust has been associated with health
issues due to the natural chemicals in the wood and substances in the wood, such as bacteria, molds, or fungi. According to the International Agency for Research on Cancer, wood dust is considered carcinogenic to humans and causes cancer of the
nasal cavity, paranasal sinuses, and nasopharynx. Exposure to excessive amounts of wood dust is associated with irritation of the eyes, nose, and throat. It also causes dermatitis, the irritation of the skin, and respiratory problems that include
decreased lung capacity and allergic reactions.
Dust is extremely small and light weight, which means it can travel quickly and uncontrollably through the air and ventilation. Contractors are exposed immediately to dust as they do a wood floor project, but residents of connected apartments, condos,
and townhouses are also at risk for exposure if the proper steps are not taken.
Dust accumulation can be reduced by cutting or shaping the wood outside of the building and by implementing the TyKote® Dust-Free Refinishing System, an innovative wood floor refinishing system that makes it easier to produce beautiful
floors with less mess. A combination of intensive cleaning and recoating provides a very durable and protective finish for hardwood floors in 3 easy steps:
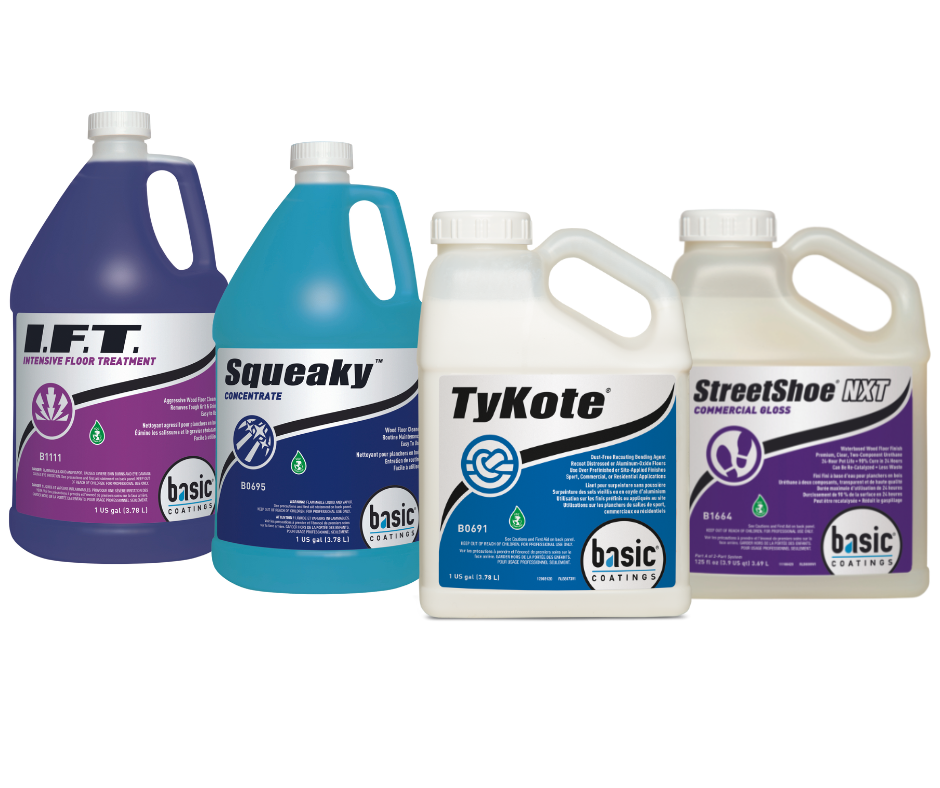
- Use Intensive Floor Treatment (I.F.T.) to clean heavily soiled
areas. Use Squeaky™ Concentrate Floor Cleaner to remove residue and prepare the floor.
- Apply TyKote Recoating Bonding Agent, which has exclusive properties that act as a
bonding agent between the existing floor and the new topcoat.
- Apply StreetShoe® NXT for unmatched beauty and durability.
Other Considerations
To ensure the safety of everyone regarding stain and dust exposure, contractors should be educated on the type of wood being used, the type of stain being applied, and all hazards associated. For both stain and dust, it is important to have an appropriately
designed industrial ventilation system that has a local ventilation exhaust and high-efficiency particulate filters. The proper personal protective equipment should be worn, which include protective clothing, gloves, and respiratory protection.
Contractors should also be trained on how to prepare a space to be safe for building occupants and themselves, which includes ventilation and personal protective equipment.
When it comes to wood floor projects in residential complexes that are in close quarters to neighbors and other residents, it is important to take the proper precautions to ensure everyone’s safety is not compromised. For more
information about HyperTone Stains, click here. For more information about the TyKote Dust-Free
Refinishing System,
click here. To get in touch with a Basic Coatings representative, click here